Kajima Corporation (President: Hiromasa Amano), together with Denka Company Limited (President: Toshio Imai) and Takenaka Corporation (President: Masato Sasaki), is developing this technology as the managing company of a consortium implementing the New Energy and Industrial Technology Development Organization's (NEDO) “Green Innovation Fund Project—Project for Development of Concrete Manufacturing Technology Using CO2—”. As the first result of these efforts, CUCO-SUICOM Formwork, which is made of carbon-negative concrete that emits virtually zero or less CO2 during the manufacturing process, has now been applied to construction sites for the first time.
The CUCO-SUICOM Formwork is made of concrete that contributes to achieving carbon neutrality by 2050 by improving on CO2-SUICOM, a technology developed by Kajima Corporation and others that fixes CO2 in concrete and enables further reduction of CO2 emissions. Recently, the Ministry of Economy, Trade and Industry (METI), NEDO, and the Ministry of Land, Infrastructure, Transport and Tourism (MLIT) collaborated to apply the CUCO-SUICOM Formwork as a buried formwork*1 in the construction of a water discharge tunnel ordered by MLIT, which reduced CO2 emissions by 677 kg/m3 compared with the use of conventional high strength panels, achieving a carbon negative of -62 kg/m3 in real emissions.
*1 Buried formwork is a formwork that is used as part of the structure without being removed after concrete is placed.
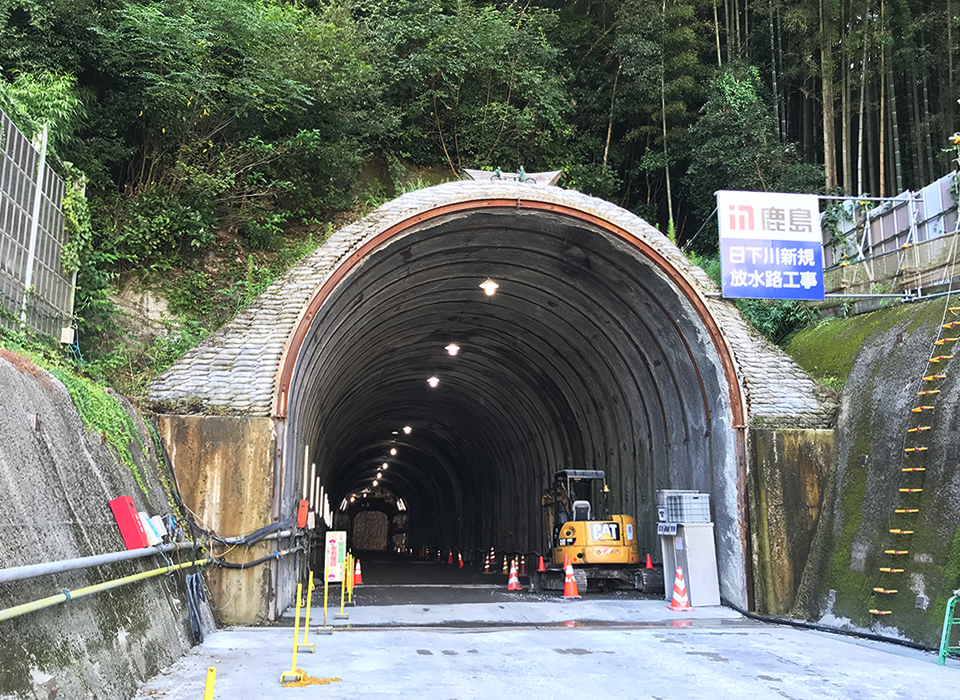
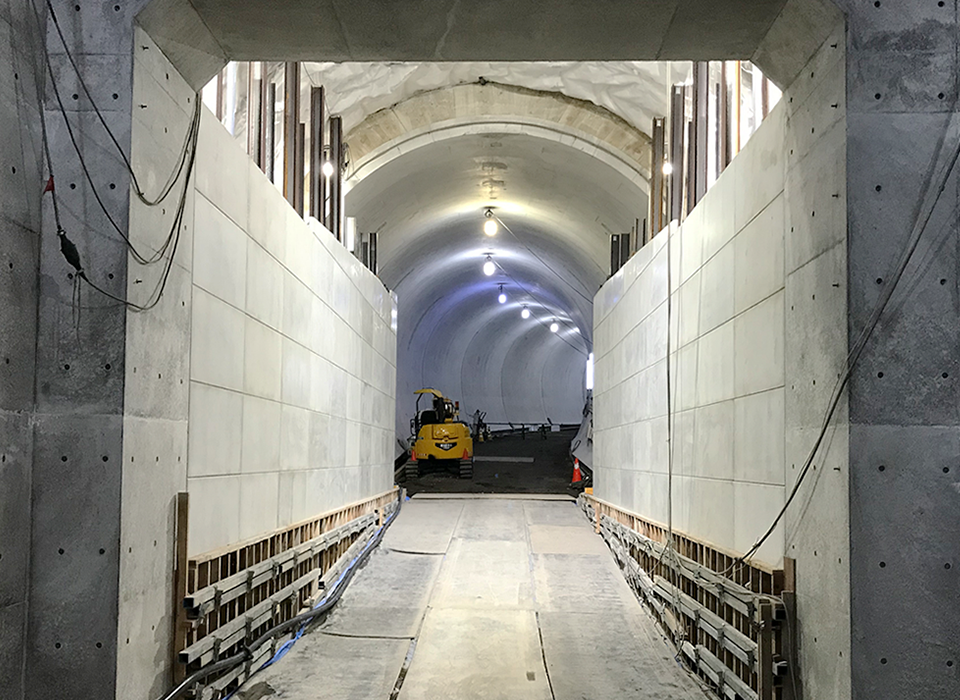
Overview of concrete used for CUCO-SUICOM Formwork
CO2 reduction and fixation are maximized by combining the two technologies of CO2-SUICOM, which reduces CO2 by replacing part of the cement with industrial by-products[1] and CO2 absorption and fixation in concrete through carbonation curing using a special admixture (γ-C2S)[2], with calcium carbonate, a CCU (CO2 capture and storage) powder[3].
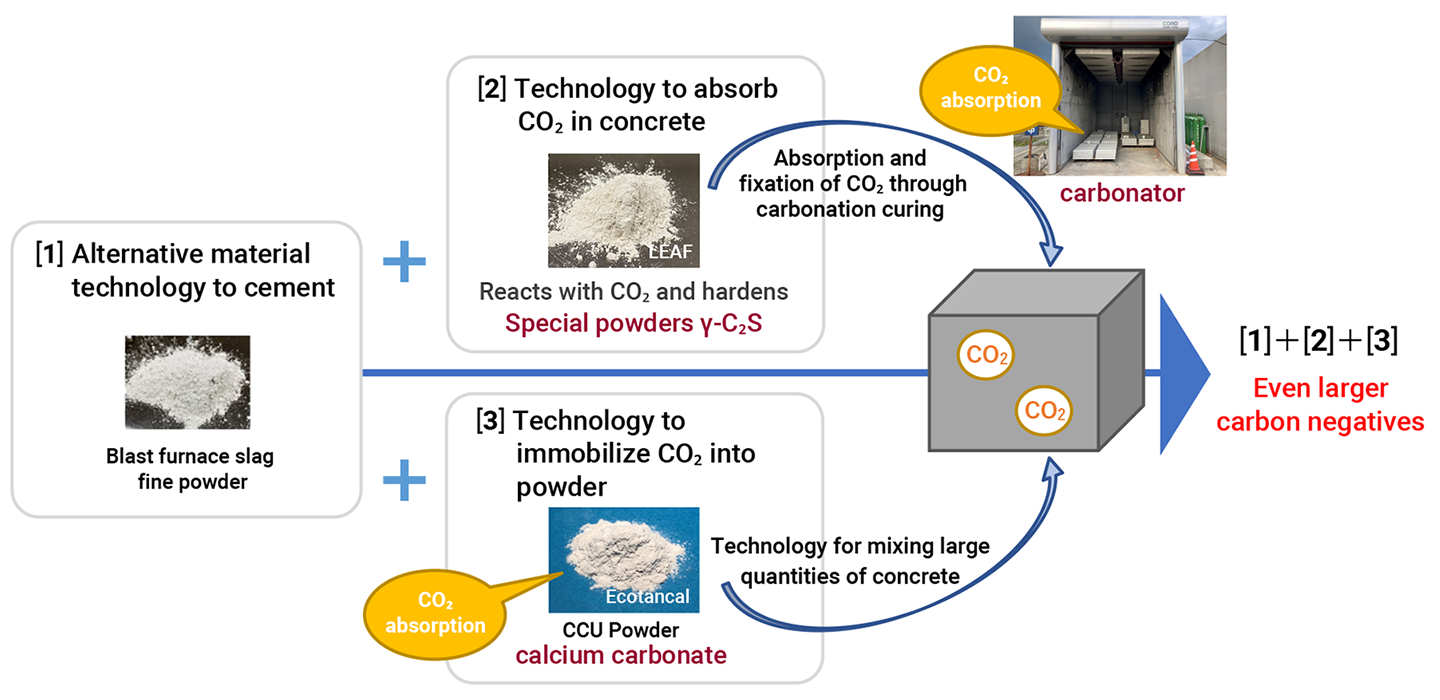
Application to actual construction
This time, “CUCO-SUICOM Formwork” was applied as a buried formwork in Spillway Tunnel Construction. Among concrete materials, replacing cement with blast furnace slag fine powder, an industrial byproduct, reduced CO2 emissions by 409 kg/m3, and using special admixture γ-C2S and calcium carbonate successfully absorbed and fixed 268 kg/m3 of CO2, for a total reduction of 677 kg/m3 of CO2 emissions. As a result, the new panel has achieved -62 kg/m3 of CO2 emissions, which is less than zero in real terms, compared to the use of ordinary high-strength panels (615 kg/m3 of CO2 emissions).
Since one cedar tree absorbs approximately 14 kg of CO2 per year, this reduction is equivalent to the amount absorbed by 139 trees.
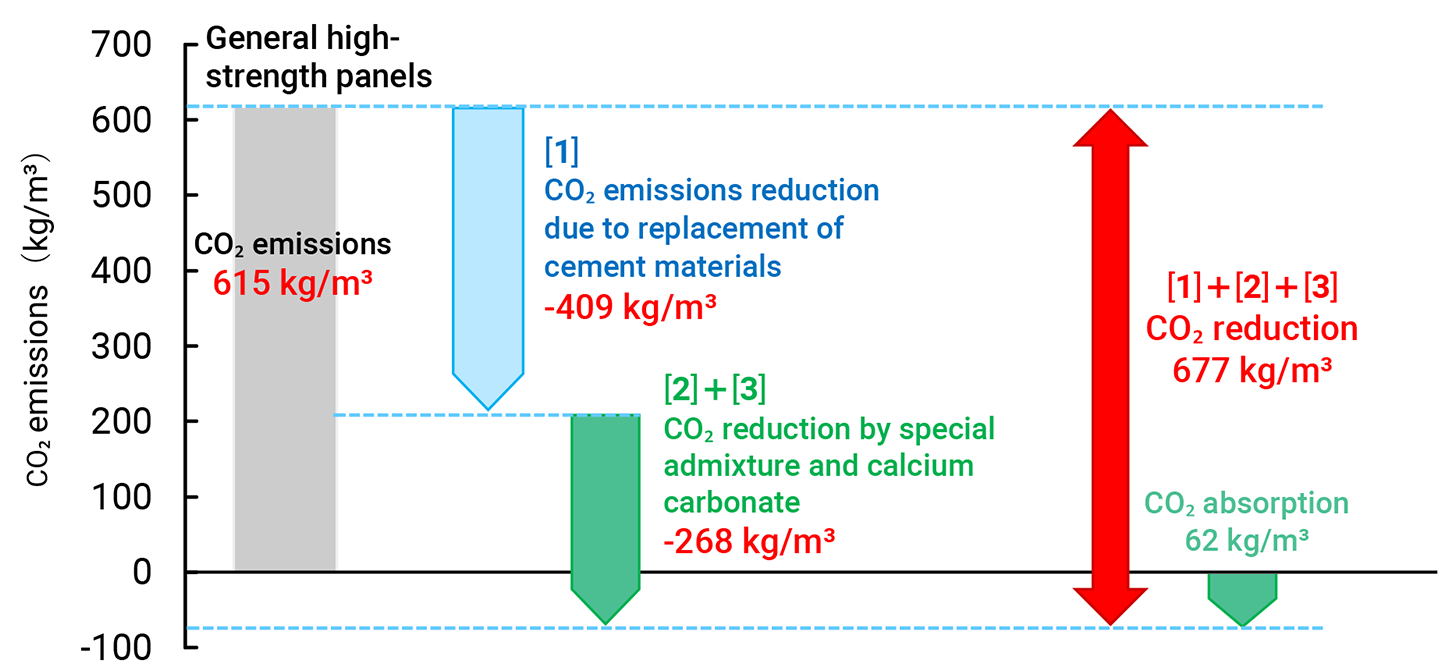
Buried formwork construction flow
[1] Buried formwork is joined together with steel to form a large format
[2] Erection of large-sized buried formwork
[3] Placement of concrete on back of buried formwork
![[1] Assembly of burial formwork](/pressrelease/img/img_20221116_05.png)
![[2] Construction](/pressrelease/img/img_20221116_06.png)
![[3] Placing of concrete](/pressrelease/img/img_20221116_07.png)
Future Development
The Consortium CUCO will continue to work in unison to develop and improve CO2 reduction and fixation technologies to achieve further CO2 reduction, thereby contributing to the transition to a decarbonized society.
Outline of Construction
- ・Construction name:
- 2021-2022 Kusaka River new discharge channel control road maintenance work
- ・Construction site:
- Okina, Hidaka-mura, Takaoka-gun, Kochi, Japan
- ・Client:
- Ministry of Land, Infrastructure, Transport and Tourism Shikoku Regional Development Bureau
- ・Constructor:
- Kajima Corporation
- ・Use :
- Discharge tunnel
- ・Construction specifications:
- (Operation tunnel) 224 m, (Tunnel gate) 1 set
- ・Construction period:
- March 2022 - March 2023